
IMPORTANT USER INFORMATION FOR OUR DXF, SVG & CDR BASED 3D PUZZLES AND OTHER PROJECTS CLICK THIS WAY
Did you know this ? CNC = Computer Numeric Control
Welcome to, the part of our website where the curtain, like in the Wizard of Oz, will finally be pulled back to reveal the little man truly is just pulling a few levers. Here you will find CNC can be an easy, fun and enjoyable way to enhance your existing hobby or next invention be it woodworking, model making, wood carving, rocketry, boat building, steel sculpture or aero modeling. You name it! Just about any hobby, craft or creative expression can benefit from the use of Robotic CNC machine tools and an understanding of the basic principals of CNC.
New to CNC ? You are in the Right Place.
Welcome to the world of CNC! This page attempts to address the many variables that go into the successful use of CNC equipment. It does not cover everything and is in no way all there is to know but it will open the door for you.
First a CNC Machine is a computer controlled tool like a router or spindle or dremel type tool that can move by computer control in three or more axis. Usually X-Y-Z thats left, right, forward, back, up and down and now becoming common a 4th Axis or rotary aXis -A-to allow machining of a rod or cyclinder that is turned by the computer.
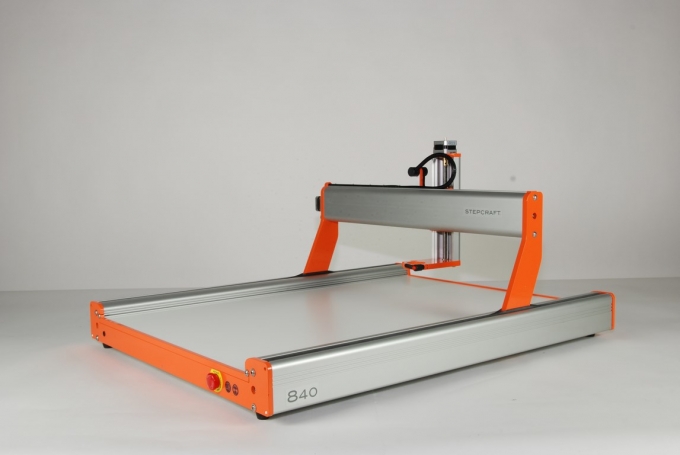
The computer code that drives these machines is called Gcode and, no, you do not need to know how to write this code to make things. CAM programs will do that for you, although in time you may want to learn it to become a CNC Guru.
Many people are making their own machines and many are commercially made at many price points. They can be found throughout the internet.
For our hobby work at makeCNC.com we use a Stepcraft 840 CNC router as shown in the picture above and a chinese made 6040 CNC Router and, at times, a Dremel tool or high speed spindle for printed circuit board routing.
we also us a 100 watt laser cutting machine 3d Taig CNC milling machine and a CNC lathe amoung others as well as small robotic Jigs to make our projects
Before we get into too much mumbo jumbo lets answer the question everyone who starts to get an interest in this hobby asks. What are the basic steps to make something with a CNC machine ? Well here they are and they are much more simple than you would think.
First, You need to have a CNC machine and driver electronics, be it commercially made or a DIY model and along with this machine you will need the correct bits to cut your chosen material. You can find more information on bit types and spindles to hold them as well as what they can cut in other places around this website.
Important note : 99% of hobby and semi pro CNC routers are not made to cut metals. If you want to cut or machine metals other than very fine soft metal sheet or PCB's (printed circuit boards )You will need a CNC Milling machine like a Taig for small parts or a Tormach for bigger parts right up to a Bridgeport for pro users.
CNC machines require a computer to supply the signals to the driver electronics in the machine to turn the motors that the machine has to cut your parts or machine your 3d art. This is called control software and most people today use the Windows based program called MACH 3 to achieve this with as little setup stress as possible.

There is more about MACH 3 in other places on our site. MACH 3 and programs like it take Gcode that is generated from your CAM software and turn it into step and direction signals that feed from your computer through a cable to the driver board or control box of your CNC machine which interprets those electrical signals into electrical pulses that drive the stepper motors on your CNC machine to turn the pulleys, belts and gears etc to move the spindle or router around to cut your parts or machine your 3d models.
Before they can do this you will need to draw your parts using a CAD (computer aided design) vector drawing software package like Coreldraw or the free Inkscape or more CNC based programs like Bobcad or Vectrics Vcarve Pro.
Some Important Notes on File Formats
The file format or file extension most commonly used to save project files from CAD software for CNC Routers is called a DXF. This was a standard used by the first CAD programs made and is still widely used today in CNC both for routers and plasma cutters as well as lathes and milling machines. A typical file would look something like this modelshipparts.dxf with DXF being the file extension name. Files with an EPS file extension are typically used by laser cutting machines. MakeCNC provides its vector based projects in both file formats to allow for as many types of CNC tools as possible to make use of our project files. 3D printers use yet another type of file format called an STL. You can find out more about 3d printers and their files in the 3D printing section of our website here Print3D
There are many other scalable vector file formats and 3D model formats in existence and you can import many types into your given (good quality) CAD software and export out your DXF and EPS files. But be sure that they carry with them the correct scale information from the original file you have or you may need to rescale your project to make it usable for CNC. This area, like Gcode post processors, can get to be a science which is why we try to keep it simple here at makeCNC and create files that you can easily use with most CAD CAM apllications. For our 2D and 2.5D work we use Vectrics Cut 2D software. Its priced under $200 and is worth every penny. We also use Vectrics Vcarve Pro software for more advanced design work and machining strategies. The Cut2D software program is the best budget solution if you want to just create basic geometry and toolpaths. Vcarve Pro is more advanced and allows many other features for design work and drawing as well as the CAM features. There are many other options for this type of work available. Some are free and some are expensive but for user friendliness and price point value you just can't beat the Vectric products. We do not sell them as Vectric have an inhouse policy but we love their software tools so you know you can trust our wisdom on this.
A quick Word on Post Processors
Many years ago in the days of the industrial Giants of CNC most, if not all, companies used special propietary electronics and control systems for the CNC machines they made. This meant that when it came time for the designer to write the Gcode to drive the machine to make a part, yes, that's right, type out the actual lines of Gcode. In those days there were no CAD programs. Each movement of the tool had to be wirtten in as a series of Gcode commands, usually in a text file or even a ticker tape, that the machine could interpret. So they had to write codes into those command strings that set the stage for the their given machine to understand the code coming after those commands. One example of this would be Fanuc's proprietary robotics control systems, which is still in use today. These codes or snipets of programming are called Post Processors and are made for specific CNC machine tools to allow the many CADCAM programs on the market to output code that their given machines electronics can understand. So as time went on and Humans created software to draw vector lines (CAD CAM) to interpret those vector lines into Gcode. Then people had to write lots and lots of little sets of codes (post processors) that the CAM program could use to set the Gcode up for use with a given brand of machine. Now that's a lot to remember but lucky for us things have changed.
With the computer revolution came chips (intergrated circuits) to drive stepper motors that understand a common set of codes called step and direction signals and some really smart people wrote software for those chips and a standard among hobby and semi-pro to pro-users started to evolve. The two main programs in use today by most hobbyists and many semi and professional users are the inexpensive but very powerful windows based MACH 3 control software which is very user freindly and the also powerful but not so user friendly FREE Linux based system Called EMC2.
The important thing is that most, if not all. CAD and CAM programs available today support MACH 3 with good post processors and many also support the Linux system. This is critical to you as the hobbyist and end user as it would would be a daunting task to write thousands of lines of Gcode for a 3D file to machine a simple leaf pattern so we bow to those who came before us.
You can imagine the amount of lines of code a 3d printer would need if written by hand to print a model of a simple plastic dog. It's scary.
Full 3D and 3D Bas Relief is a Different Story
If you want to do 3D relief carving then it gets a little more complicated and you will need other types of software like Meshcam Art and 3D modeling pakages like Hexagon. See our (3d primer page here)
Last, but not least, you will need a CAM software package to turn your drawings into Gcode that you feed into the MACH 3 software or control software you have chosen to use. The CAM (computer aided manufacturing) software creates toolpaths for the router to follow and makes them into Gcode which is a set of mathtimatical corrdinates that Mach 3 interprets into signals for the motors of your machine.
So here it is in Sequence.
1: You draw your part in the chosen vector based CAD drawing program. Vectors are lines the tool can follow unlike raster or photo editing programs like Paint or Photoshop that manipulate pixels or dots that make up an image.
2: You import that drawing, usually in DXF format, into your chosen CAM program.
3: You export that Gcode from the CAM program and put it on a memory stick and then head off to your shop where you plug in the stick to the computer that is connected to your router and setup with your control software. In this case we assume MACH 3, as you would have chosen that option when you exported your gcode from your CAM software. You then import the Gcode, load the code into mach 3 and run the file to set the wheels in motion on your CNC tool. Of course we trust you have the right bit in the router for the cut you want to make and that you have homed your machine correctly and you have the material fixed down to the table surface correctly remembering to make sure you do not have screws or clamps that will get in the way of the toolpath you have created.
All things being equal, if you have followed your procedures correctly and have been carfeul in your planning and fixturing then you should be good to go.
Always wear safety glasses and keep your hands and hair away from the running tool. CNC machines can and will injure you badly so ALL Safety Measures MUST be used.
A big red stop switch is Essential and watch for flying parts if you do not have your material hold down well thought out.
Bridges in your Parts Might be a Thought.
Homing the machine is where you set a place that is the starting point for the router bit and the machine references all moves after that from that point. Think this through and you will see its wisdom.
Also, again, Be Careful in your toolpath planning to make sure you do not put screws or clamps in the way of the toolpath or moving tool bits.
Simulate your tool path in MACH 3 to check before running the actual cut sequence
Here are a few other things to consider below but if you have got this far you are well on your way to CNC heaven. Enjoy!
Before making a purchase of CNC equipment, there are several things to consider. First, you should define your requirements, then you should review products, and finally you should begin shopping for a machine or parts to build one.
Don't forget! Here at makeCNC we have created many ready-to-cut projects for your CNC enjoyment. We do the hard stuff and you can create Great, Useful and Fun Projects at a cost that won't break your budget. You can browse our online store here -

IMPORTANT USER INFORMATION FOR OUR DXF & EPS BASED 3D PUZZLES AND OTHER PROJECTS CLICK THIS WAY
Requirements
There are several requirements that you need to consider when selecting or building a CNC machine.
-
What is the application you are going to be using a CNC machine for? What types of materials do you plan to cut? How large are the materials you need to cut? What type of cut do you need (will it be 3 axis or more)?
-
What level of precision is needed? Wood workers are typically used to achieving 1/16" tolerances. Do you need more precision?
-
What speed (inches per minute) do you need the machine to go? Typically manufacturers try to balance the trade off between speed and precision. Machine speeds are all over the map.
-
What is your level of comfort/knowledge with similar types of tools?
-
What is your level of comfort/knowledge with a personal computer? Specifically, how much do you know about 2d and 3d cad packages? If you are not very comfortable with them, do you have a resource that can help?
-
Determine how much you want to spend up front.
-
How should I fixture the item I want to cut?
Review Products
There are literally hundreds of CNC machines on the market today. They come in all types of shapes and sizes. Some are designed for specific applications while others are more general purpose in nature.
Many people are building their own machines from scratch and the internet is full of support for this.
There are several steps required to begin using your CNC machine successfully.
Set-up
Setting your machine is critical to early success. Make sure the platform is stable and your CNC machine is secure. The less movement that occurs the better.
Material Selection
The right material in the right size and thickness are all important attributes to consider.
Fixturing Selection
Appropriate fixturing (securely fastening to a cutting surface) of an item to be cut, plays a key role in the success of any project you undertake. Without proper fixturing, you will break more bits, produce inferior and inaccurate cuts and tasks will take longer to complete than necessary.
Fixturing Types
There are several different approaches to fixturing including adhesives, glue, and mechanical.
Adhesives
Adhesive fixturing uses double sided tape of various sizes and strengths to bind the item to be cut with the CNC cutting surface. The strength of this approach is that it is quick and cheap. It requires little to no preparation time to accomplish. The weakness of this approach is that it can be difficult to separate the item cut from the CNC cutting material. This is especially true on thin cut items. We have had some of our finished items break in the process of being separated. Another weakness is that it's a pain to clean up the backside of the cut item were the adhesive was placed. In some cases, a clean underside is not important. In others, it is critical. Depending upon the surface of the cut item, we have tried paint scrapers, mineral spirits, and acetone with mixed results.
Glue
Another approach is to use SuperGlue. This approach is largely practiced by people cutting metal and circuit boards. Depending upon the material to cut it or may not be the best approach. Once the cut has been completed, simply douse the item with acetone to loosen up the SuperGlue.
Clamps
A third fixturing method is clamps. While the simplest to use, they can be more trouble than they are worth. Clamps must stay out of the way of all moving parts of the CNC machine. Unlike the previous fixturing methods, there is no clean-up activities required.
Mechanical
A fourth approach is to use mechanical fixtures. Mechanical fixtures require more upfront planning than any of the other methods. Some CNC machines come with pre-drilled holes for adding fixturing, some do not. In one of our machines, we added an MDF board and placed holes and screw backing every six inches. With mechanical fixtures you can use screws and washers, boards and several other items as hold downs. There are no clean-up activities required.
Bit Selection
From a bit perspective, we recommend you start with larger sized bits. They are cheaper and tend to break a little less than the smaller bits. Once you get the hang of it (count on a month or so) get some smaller bits as needed for your desired application.
makecnc has a great selection of bit sets for all types of work here in our CNC tool section of the webstore.
Some other things to think about
-
Type of cut
-
Type of material to cut
-
Machine type
-
Spindle type
-
Depth of cut
-
Feed Rate
-
Spindle Rate
-
Type and size of bit
Thanks for visiting makeCNC. We hope you found this information useful. We will add to this page as time goes by. Come again soon!
Enjoy the rest of our site!
Thanks
Paul & Julie
IMPORTANT USER INFORMATION FOR OUR DXF SVG,CDR BASED 3D PUZZLES AND OTHER PROJECTS CLICK THIS WAY


YOU DO NOT NEED A PAYPAL ACCOUNT TO PURCHASE AT OUR STORES!
Don't have a PayPal account? JUST CHOOSE at the PayPal checkout page to make a onetime credit card or bank account payment.
|